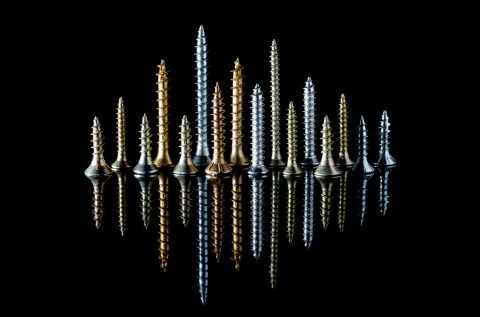
Table of Contents
- What Are Construction Screws?
- Sharp Point Screw Production Process
- Drill Point Screw Production Process
- Why Different Production Processes?
- Conclusion
Construction screws are key parts in building projects, woodworking, and industrial setups. They may look simple, but making good construction screws needs careful steps and special tools. In this guide, we'll look at how construction screws are made, and why sharp point and drill point screws are made differently.
What Are Construction Screws?
Construction screws hold building materials together. They're stronger than regular home screws because they need to handle more stress, weather, and provide long-term strength. They come in many designs, materials, and finishes for different building jobs.
The main types are:
- Sharp point screws (drywall screws): Used for wood, drywall, and general building
- Drill point screws (self drilling screw): Designed for penetrating denser and harder building materials, such as metal or high-density boards
Each type needs a different making process to work well for its job.
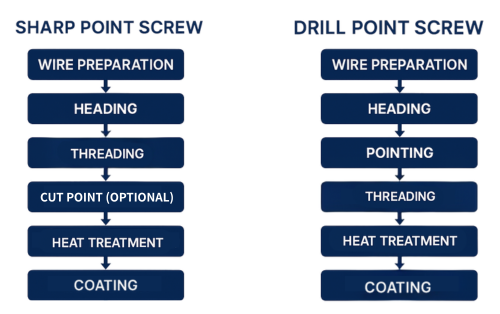
Sharp Point Screw Production Process
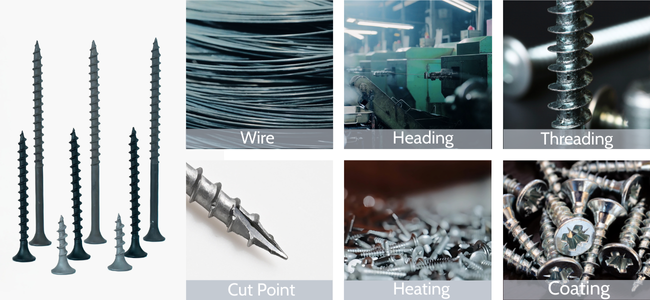
Sharp point screws are often used in woodwork, building, and general construction.
1.Wire Preparation
First, workers select low-carbon steel wire or other right metal based on the screw's application and required strength. The wire, which is free from radiative contamination, is then prepared for forming.
2. Heading
Next, machines press the wire to make the screw head. Strong presses shape the metal into flat, pan, bugle, or hex heads, based on what the screw needs to be.
3. Threading
Special dies put pressure on the metal to roll threads onto the screw. This makes the spiral ridges that help the screw grip without cutting the metal, so it stays strong.
4. Cut Point (When Needed)
Some sharp point screws get more changes like Type 17 cut points, which have slots at the tip to stop wood from splitting.
5. Heat Treatment
To make screws hard and tough, they go through careful heating and cooling, which makes them stronger.
6. Coating
Workers add protective coatings like zinc, phosphate, or other finishes to stop rust and make screws look better.
7. Quality Control
Comprehensive testing is conducted not only for visual appearance but also for functional performance, including penetration tests and any specific requirements provided by the customer. Driving performance, thread accuracy, point shape, and coating quality are all verified before final approval.
8. Packaging
Approved screws are sorted, counted, and packaged according to customer specifications, ready for shipment.
Drill Point Screw Production Process
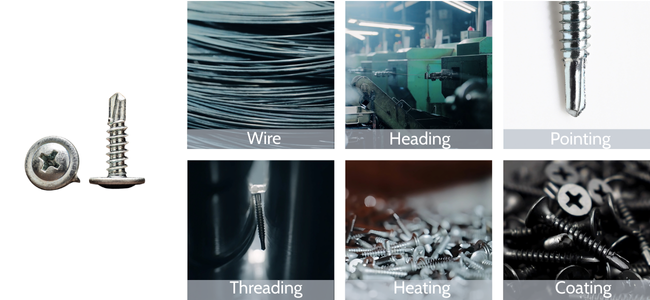
Drill point screws are primarily used for metal and other high-density building materials.
1. Wire Preparation
Like with sharp point screws, the process starts with picking the right wire, but often with different materials to handle the drilling job.
2. Heading
Cold presses form the screw head based on plans, making drive styles that can handle more turning force.
3. Pointing
Unlike sharp point screws, drill point screws go through a special pointing process that makes a fluted drill tip that can bore through metal. This step leaves extra material (leftover) at the tip.
4. Thread Rolling
Threading is done after pointing. This step removes leftover material from the tip and forms accurate threads while preserving the shape of the drill point.
5. Heat Treatment
Careful heating and cooling makes the right balance between hardness for drilling and toughness to prevent breaking.
6. Surface Treatment
Rust-fighting coatings are added to protect the screws from weather and make them last longer.
7. Quality Control
Comprehensive testing is conducted not only for visual appearance but also for functional performance, including penetration tests and any specific requirements provided by the customer. Driving performance, thread accuracy, point shape, and coating quality are all verified before final approval.
8. Packaging
Finished screws are sorted, counted, and packed based on specs for shipping.
Why
Different Production Processes?
The key difference between making sharp point and drill point screws is the order of the pointing and threading steps. This change in order is not random but has an important technical reason.
For Drill Point Screws:
- Pointing Before Threading: The pointing step makes the special drill tip but leaves extra material that could mess up drilling.
- Threading After Pointing: The thread-rolling step removes this extra stuff while making threads, keeping the drill point shape right.
- Better Performance: This order keeps the drill tip good at cutting through metal without needing a starter hole.
For Sharp Point Screws:
- Threading Followed by Tip Shaping: Since sharp point screws do not require a fluted drill tip, their pointed ends are simply shaped after threading. Minimal material is removed, and there’s no need for post-point cleanup.
- Simpler Manufacturing Flow: This order lets production flow better without losing quality.
- Different Job Needs: Sharp point screws are used for wood, drywall, and general construction — focusing on easy penetration and holding power, rather than drilling through metal.
Understanding these making differences explains why some screws work better for certain jobs and helps builders pick the right screw for each task.
Conclusion
Making construction screws needs good engineering, metal knowledge, and quality checking. Each step from picking wire to final packing is important to create screws that builders can trust for important projects.
Whether you're working with wood, metal, or mixed materials, using the right construction screw makes a big difference. Now that you know how these important fasteners are made, you can make better choices for your next building project.